Trackwise’s Improved Harness Technology™ (IHT) builds on the space-, weight- and cost-saving attributes of flexible printed circuits (FPCs) to meet interconnect challenges presented by advanced medical applications that demand extended connection length, high reliability, bio-compatibility, and support for integrated smart features.
Smarter Medical Technology
Today’s medical technology is becoming ever smarter, from processing-intensive imaging systems, to smart wearable monitoring devices, to cutting-edge research equipment. Increasing sensitivity and intelligence requires greater connectivity to handle the control signals and feedback data, and to provide power. Conventional wire harnesses, coupled with high-quality connectors designed specifically for medical applications, have traditionally handled this task adequately. However, as medical technology continues its mission to improve standards of care, help treat more conditions, and improve patient outcomes, connectivity must satisfy new technical demands. Miniaturisation is a constant demand, but today’s medical interconnect solutions must also feature greater flexibility to connect moving parts, and extra length to reach smart circuitry in large items such as full body scanners and surgical robots. Increasingly, medical connectivity solutions must also integrate intelligent functionality and handle more signals, more bandwidth, and more power.
New alternatives that can fulfil these emerging demands while at the same time elevating performance and reliability are needed.
Next-Generation Interconnects
Flexible printed circuits (FPCs) are commonly used in space-constrained applications such as mobiles and DSLR cameras, as they offer considerable space and weight savings over wire harnesses. FPC technology is mature and it can be produced to high quality standards in many locations worldwide. Unlike the conventional wire harness, FPCs do not necessarily need associated connectors. Whilst often connectors are used, in other applications the FPC can be integrated within the system to directly link system elements. Another benefit is that the typical FPC manufacturing processes minimises human intervention, whereas conventional wire harnesses are often very manual-labour-intensive. This can boost production quality and efficiency, eliminate human errors and result in manufacturing time and cost savings.
A typical FPC stack-up comprises a polymer carrier and a conductor layer, which is usually etched copper. The most basic FPC combines one layer of each type and can have a thickness of 25µm or less. A cover layer may be added to protect the conductor. Successive copper and dielectric layers can be added to create multilayer interconnects. Plated-through holes may be used to connect conductors in different layers, if needed, and terminations can be applied on one or both sides. FPCs can combine the functions of a PCB and interconnect in a single part, which can simplify the assembly of the final product and enhance reliability.
Therefore, FPCs deliver many of the characteristics needed to realise the next generation of advanced medical systems and devices, including mechanical flexibility, increased interconnect density and bandwidth, and the ability to include built-in intelligent functions.
However, traditional FPC production processes that use sheet materials typically restrict the maximum length to about 600mm. A small number of producers can supply lengths up to about two metres. Trackwise’s patented Improved Harness Technology™ (IHT) is a roll-to-roll manufacturing process, performed using advanced machinery and custom software, that allows interconnects of practically unlimited length to be produced (figure 1). These can address the most demanding applications in large items of equipment such as full body scanners and industrial robots.
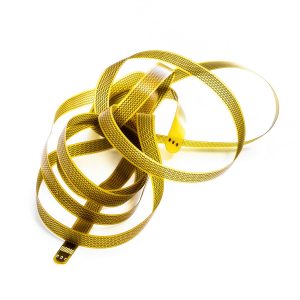
Image | Figure 1 (Trackwise)
Several medical device makers have already selected FPCs made using IHT for catheters. Other medical applications include endoscopes, and related devices such as coagulators that are passed through the endoscope to cauterise bleeding tissue or for treating small cancers and polyps. These applications require properties such as minimal thickness, flexibility, reliability, high strength, and bio-compatibility. As reported in the Journal of the American Heart Association, new developments in catheters, endoscopes and other medical equipment are “allowing the operator to work with the patient’s anatomy rather than fighting with it“.
With the ability to integrate electronic components as an intrinsic part of the interconnect, IHT enables new, smart functionalities in medical devices such as catheters and endoscope. These types of instruments are the underlying enablers for minimally invasive surgery (MIS), which is known to help reduce in-patient time, surgical risks, patient trauma, and recovery times. Traditionally, their roles have been in draining fluids from the body, to administer medicines internally or for localised anaesthesia at a specific nerve junction, as well as to assist inspections such as angiography, and to enable surgical procedures such as angioplasty and cardiology.
Small devices such as miniature cameras and lighting can be built-in to help users visualise the procedure and progress. Integrating these, as well as miniaturised signal and power connections, within an instrument that typically has overall diameter between 1.6mm and 2.3mm presents challenges to conventional wiring techniques. FPC interconnects simplify design and manufacture, enabling interconnects to be chosen purely on the basis of electrical properties without dependence on mechanical strength. Trackwise’s IHT enables interconnects of any length thereby enabling designers to avoid using joints and connections that can otherwise compromise strength, reliability and suitability for medical use.
A single FPC can replace multiple microwires thereby simplifying the integration of sensors and actuators. This makes it possible to drive extra intelligence into catheters, such as additional temperature sensors and MEMS sensors to monitor pressure against the catheter sheath for safety purposes or to check for correct orientation of an inserted surgical instrument. Using this approach, smart catheters can provide more sophisticated functionality and capture multiple data channels during a procedure, to enhance patient monitoring and welfare as well as for record keeping and training. IHT is also ideal for producing specialised catheters of extended length, for users such as equine vets.
Trackwise can also supply IHT interconnects to manufacturers of large slip rings for full-body scanners. The combination of slip-ring properties and long, flexible FPCs produced using IHT ensure continuous power and signal connectivity as the imaging subsystem rotates 360° around the patient in a full body scanner.
FPCs are also being considered for an advanced neuroelectronic interface to cure brain disorders. Researchers are developing the interface using graphene electrodes to ensure minimally invasive contact with targeted locations in the brain and have identified an opportunity to incorporate advanced, flexible interconnects between the electrode array and signal-processing equipment, leveraging IHT.
IHT Key Requirements
Trackwise’s IHT roll-to-roll fabrication process can create length-unlimited interconnects for numerous applications across sectors such as aerospace, industrial, and automotive, in addition to medical devices including veterinary equipment.
The process is compatible with a wide variety of material technologies, which allows flexibility to fine-tune the substrate properties to meet exacting application requirements. Trackwise has established a large and growing knowledge base about materials such as Fluoro ethylene propylene (FEP), which has several outstanding characteristics including bio-compatibility as well as UV and chemical resistance, and excellent low-temperature performance. In addition, FEP can be welded and moulded, unlike other fluoro-plastics such as PTFE.
Clearly bio-compatibility is a key concern in medical applications, particularly where equipment is intended for direct body contact. Trackwise also has knowledge specific to the use of gold and palladium for body contact and internal use. The company is working towards achieving ISO 13485 certification to help further simplify and streamline product approval processes for customers in the medical field.
Conclusion
As the variety, features, and performance of advanced medical devices continue to grow, equipment designers need connectivity solutions that deliver mechanical flexibility with superior performance and reliability. Medical devices that are in widespread use, such as catheters, face demands to become smarter as well as safer, while innovations at the leading edge of medical research need high-performing production-ready processes to help make the leap from the lab into hospitals and healthcare practices for the good of all.
IHT combines the known advantages of flexible printed circuits (FPCs) with innovative production processes to enable length-unlimited interconnects for applications in multiple sectors. Trackwise’s knowledge of suitable bio-compatible materials and experience in applications such as catheters and probes, enables IHT interconnects to meet the needs of demanding medical applications.
By Philip Johnston, CEO, Trackwise